The Benefits of Predictive Maintenance
Add bookmark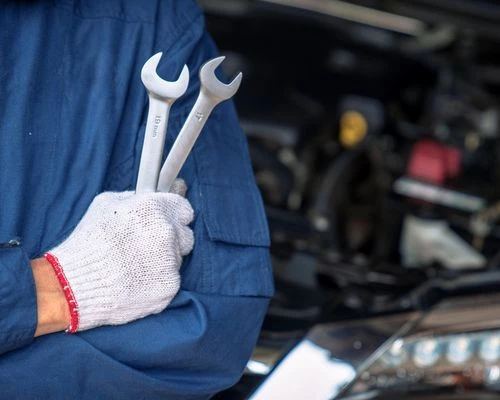
Predictive maintenance uses advanced data analytics to analyze trends, detect problems and propose maintenance actions before a problem causes a stoppage on the line.
Unplanned downtime costs companies up to $50 billion per year, according to WSJ; equipment failure accounts for nearly half of unplanned production outages. Keeping equipment in good working order is not only important for the bottom line, it also helps to keep staff safe and production working efficiently.
In the oil and gas industry, unplanned failure hurts not only production, but can have an outsized safety, social, and environmental impact.
There are 5 main types of maintenance strategies that organizations typically use. These include:
Reactive maintenance: Repairing a piece of equipment once it breaks down or a problem is identified.
Predetermined maintenance: Following an equipment manufacturer’s advice about key maintenance and servicing dates.
Preventive maintenance: Having a regular schedule of inspections and tasks on an asset to keep the machine in good running order.
Condition-based maintenance: Fixing and repairing equipment when it reaches a certain condition (such as number of hours of run time, temperature, or age). Condition-based maintenance requires ongoing monitoring and tracking of equipment.
Predictive maintenance: This is a more sophisticated version of condition-based maintenance. Trends in machine performance and break downs can be analyzed to identify common sources of failures and propose optimal maintenance schedules and routines.
Many of the oil majors have deployed predictive maintenance approaches at some of their production facilities. In 2019, for instance, ExxonMobil announced a partnership with Microsoft to transform operations in the Permian basin. By storing data in the cloud, engineers, scientists and analysts would be able to leverage machine learning to minimize downtime and increase productivity by enabling machine learning and predictive maintenance.
“There is ripe opportunity for the energy industry to transform how we leverage our data flows,” said Anish Patel, ExxonMobil’s Permian technology integration manager, quoted in the company's Energy Factor magazine. “What was possible 10 years ago is nothing like what we’re doing today, and that trend of rapid innovation will only exponentially accelerate going forward.”
Predictive maintenance is effectively the “goldilocks” version of maintenance. It’s neither too much nor too little, but just right.
It helps companies get smarter about what they do and when, and helps to warn of problems. That helps companies save time and money by carrying out tasks only when they are necessary but before it has affected production.
Deloitte estimates that the gains from predictive maintenance are enormous: lowering maintenance costs by 25%, increasing productivity by 25%, and reducing breakdowns by 70%.
Another study, conducted in 2013 by Solomon RAM, found that fourth quartile companies spend nearly four times more on maintenance than top quartile companies that focus on using the tools of predictive maintenance.
How predictive maintenance works
In many modern oil and gas companies, machines with special IoT enabled sensors can provide a flow of data in real-time about equipment variables such as temperature, humidity, vibrations, pressure levels, light levels and more.
As this data is transmitted in real-time over networks, the system can alert operators to potential problems such as a machine getting too hot. This can then be used for the operator to take corrective action.
However, an even more powerful approach is using this data to analyze trends over time and identify the common failure modes. By learning what conditions (temperature, pressure, vibrations) precede an equipment failure, manufacturers can identify patterns and define appropriate actions.
Conclusion
Oil and gas companies are likely to employ different maintenance strategies based on the type of asset and how critical it is to production processes. For some types of equipment that have minimal impact - a lightbulb, for instance - a reactive maintenance approach is perfectly acceptable. Fix it when it’s broken.
However, for business-critical assets, a more intelligent approach that makes use of cutting-edge data and analytics to optimize maintenance schedules can save oil and gas companies time and money. Predictive maintenance offers a practical and proactive approach to keep your machines running at peak performance.