Driving Innovation: Covestro’s Journey with Digital Twin Technology
Covestro's Process Data Analytics & Condition Monitoring Lead on optimizing asset performance and reinforcing data-driven operations.
Add bookmark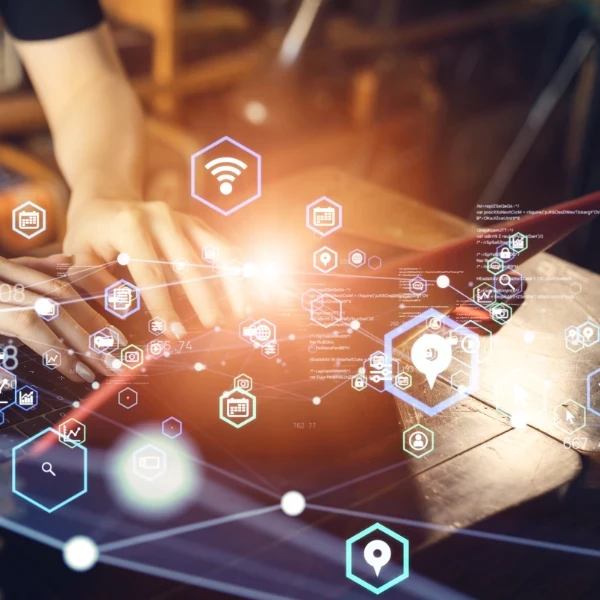
As one of the world’s leading manufacturers of high-quality polymer materials and their components, Covestro is known within the industrial sector for consistently pushing boundaries through digital transformation and innovation. Having already made considerable progress in digital advancement, the company is now rolling out Digital Twin technology [Covestro Monitoring Platform] at all major locations, aiming to support safe, reliable and efficient production. This initiative will enable key stakeholders to have timely access to information to make decisions on critical production assets.
Ahead of the Connected Worker: Energy Summit, we spoke with Bharat Marwaha, Global Product Owner for Covestro's Monitoring Platform, to learn more about driving digital innovation through Digital Twin technology. Bharat has been actively engaged in driving digital transformation in the process industry for over five years, with diverse experience in establishing global asset monitoring platforms, analyzing time-series data, and creating visualizations.
From the critical asset selection process to managing operational complexities and leveraging existing software, read as he highlights how Covestro is optimizing asset performance and reinforcing its commitment to reliable, data-driven operations.
Maryam Irfan, Connected Worker Series: Can you talk to us about where you are in the Digital Twin implementation journey?
Bharat Marwaha: We started the program a few years ago with a very holistic approach, and that included a roll-out strategy with three regional hubs: NAFTA, EMEA and APAC.
We began the deployment in the NAFTA region, where we are currently further along. Recently, we started rolling out the digital twin deployment in Europe, and the plan is to extend this deployment to Asia either later this year or early next year.
Maryam Irfan, Connected Worker Series: What would you say was the key driver behind the implementation of digital twin technology at Covestro?
Bharat Marwaha: The key driver for us was reliability. We wanted to minimize unplanned events, especially since we operate a large continuous manufacturing sites. In this industry, even one day of production loss due to an unreliable asset causing an unplanned shutdown can cost the business millions of dollars. Hence, the focus on reliability has been essential for us.
Maryam Irfan, Connected Worker Series: What were the biggest challenges you faced during the initial implementation of digital twin technology at Covestro, and what have been the key learnings so far?
Bharat Marwaha: The first step is to identify and shortlist critical assets for deploying digital twins. The next step is determining which of those assets have the right instrumentation or sensor coverage. This step has been a challenge to do at scale. Without the right sensors, we risk missing key measurements, which makes it difficult to assess the health of the asset or anticipate upcoming anomalies.
At the outset, it’s challenging to determine exactly what instrumentation each asset has on-site. And even if the sensors are in place, they might only be set up for local monitoring and not sending time series data to a DCS or data historian. So, during each rollout, we need to review which assets are problematic and what instrumentation is available.
These issues slow down the process, but there is no simple button you can press and get it done.
READ: Top 4 Challenges Facing Data & Analytics Leaders in the Energy Sector
Maryam Irfan, Connected Worker Series: Is there a specific procedure you follow when it comes to shortlisting assets?
Bharat Marwaha: As part of our global asset strategy, we rank assets using an industry-standard risk ranking system, ranging from high to medium to low criticality. This is based on factors like the impact of production loss and other key objectives. We also incorporate risk ranking, which is a common industry practice.
Since we already conduct this exercise within our processes, we use it to identify our critical assets. Naturally, certain units or plants experience issues with specific assets more frequently. So, within the overall critical list, we focus on those 'bad actor' assets that have shown consistent issues over the last couple of years.
“I enjoy these conferences because they help broaden my knowledge and provide insight into what other companies are doing in this space. I’m always interested in learning how our peers are approaching similar challenges, while sharing my own ideas, and gaining new perspectives.
In particular, I’m interested in seeing how other companies are integrating time-series data—such as sensor data—with other data sources, like ERP systems or safety systems. I look forward to learning more about advancements in that area.” – Bharat Marwaha, Global Product Owner for Covestro's Monitoring Platform
Maryam Irfan, Connected Worker Series: How effective was the use of digital twin technology in simulating the management of assets? Were there any unexpected limitations in forecasting potential scenarios?
Bharat Marwaha: To effectively monitor our critical assets, we examine typical assets that are not limited to a single-use case but are widely used across our plants, such as centrifugal pumps and heat exchangers. These assets are typically found in process industries and often have reliability issues. For instance, due to the nature of our chemistry, our heat exchangers tend to foul on a recurring basis. So, the unit teams are always looking for insights to help plan the next cleanings for those assets.
This has allowed us to develop a standardized approach for creating digital twins, and by modeling them on those assets, we can provide teams with guidance on maintenance, like alerting them when a critical heat exchanger might need cleaning within the next six months.
We of course encountered some challenges. For example, we assumed that a centrifugal pump would not operate during plant shutdowns, but sometimes it does—for various operational reasons—leading to a “cold-flow” operation that does not match the standard pump curve. This can cause false alarms. In the initial deployment phase, we faced some of these issues, but then we learned to filter or customize the alarms to account for additional circumstances.
Maryam Irfan, Connected Worker Series: Can you share an example where a simulation didn’t produce the expected results?
Bharat Marwaha: Going back to the example of the pump, there was a situation where we began receiving alerts indicating abnormal behavior, showing that the pump was operating far outside its expected curve. When we investigated it, we discovered that was a false alert—the unit was down, and the pump was running with a cold flow.
With cold flow, the temperature and fluid viscosity differ significantly; the fluid becomes more viscous and requires more power to operate. However, in our initial modeling and assumptions, we designed the digital twin to monitor performance during normal operating hours, not during shutdowns. To address this, we created additional logic to recognize cold-run conditions and prevent unnecessary alerts during those times.
Maryam Irfan, Connected Worker Series: How did you balance the immediate costs of digital twin implementation against the long-term efficiency gains?
Bharat Marwaha: We didn’t attempt to create a digital twin for every existing asset; instead, we focused on the critical ones—the so-called 'bad actors.' This helped us manage deployment costs, as our primary investment was just time.
Additionally, we didn’t buy any special software. We already had an existing software suite which we leveraged to create the digital twins without incurring any additional expenses. So, by using our internal software and by focusing on simulating only the most critical assets, we were able to keep costs low.
READ: Prioritizing Connected Worker Safety in Remote and Hazardous Environments
Maryam Irfan, Connected Worker Series: How long did it take to see tangible results from these initiatives? Can you share any KPIs or milestones used to measure success?
Bharat Marwaha: Measuring success from a business perspective can be challenging because if you prevent an unplanned event, you may not immediately know that it was avoided due to your intervention—since it simply didn’t occur. It’s difficult to say with certainty what stopped the event from occurring because other factors could also have played a part in preventing it.
To address this, we track and maintain a database of past incidents and associated costs. By comparing those incidents, we justify our efforts, showing that we are actively avoiding similar events. Our KPI focuses on ensuring that after rolling out these digital twins for critical assets at a plant or site, no unplanned events occur with those assets.
Additionally, we measure engagement through dashboards that track asset health, monitoring how many users actively use those dashboards and benefit from the data. We also conduct training and run regular reports on user engagement, tracking unique visitors as another KPI.
Maryam Irfan, Connected Worker Series: What are the next steps for improving and expanding the use of digital twins at Covestro?
Bharat Marwaha: The next step is to continue the global rollout. With each deployment, we learn something new and identify existing gaps, which we then work to address.
One key observation has been that, regardless of how effective a digital twin or tool may be, it won’t achieve its full potential if the end users aren’t familiar with it or don’t know how to respond. For instance, if someone receives an alert by email but isn’t sure what action to take, they may not respond in time to prevent an unplanned event.
Currently, we rely on a 'human-in-the-loop' approach because we are not yet at a point where alerts are sent directly to machines that can act autonomously—especially in our process industry, where complex chemistries are involved. This requires proper training and clear workflows to ensure that users understand their role for when they receive an alert.
To support this, we are launching a new initiative focused on developing effective workflows. While the specific workflow may vary, it is essential to establish a consistent process and ensure users feel comfortable with it.
Hear more real-word case studies from energy and utility leaders, and network with your industry peers at our upcoming events:
Connected Worker: Energy Summit
March 18-20, 2025 | Houston, TX
AI in Energy Summit
February 24-25, 2025 | Houston, TX