How to enable effective and efficient operational support with the pervasive connectivity of remote assets
In the third blog in his series on remote operations during Covid-19, OSIsoft’s Craig Harclerode reveals how to use data collected from remote assets to offer effective remote operational support
Add bookmark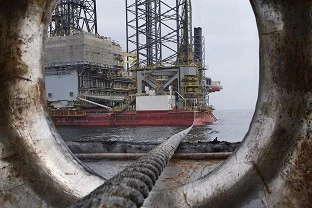
In this third blog in my series on remote operations during Covid-19, I want to focus on the importance of leveraging pervasive data collection from remote, often “dark” assets for efficient and effective remote operational support.
One common misconception is that traditional SCADA or DCS have all of the operational data and that connecting to these systems will enable pervasive remote asset data access for visualization and associated analytics.
In reality, only 50 to 80 per cent of remote operational data flows through SCADA and DCS. There is non-control data stranded in remote terminal units (RTUs) and unit and station PLC controllers. In many cases, there is no instrumentation at all on remote assets that often remains invisible to operators who solely rely on SCADA or DCS.
A best practice is to avoid relying on such systems for non-control, non-critical data acquisition. Instead, operators should rely on the PI System's pervasive data capabilities to connect to remote assets. Methods such as secure connectivity to PLCs using OSIsoft's Edge Data Store, embedded edge capabilities in OSIsoft's partner community or cloud-enabled IIOT gateway connectivity are much more efficient and are now becoming commonplace.
By adding edge data and gaining access to “dark” data, remote operational support can be much more effective and comprehensive and can deliver self-serve, contextualized access to operational intelligence.
Lighting up dark compressors
A few years ago, MPLX, a subsidiary of Marathon Oil, had a problem. The company provides natural gas gathering and processing services to E&P companies and operates 850 remote compression units for its gathering systems. However, dealing with a hard-working compressor fleet with a diversity of vintages, makes, models and limited remote connectivity posed a challenge because of limited visibility to asset performance and an inability to perform anomaly detection to obtain optimal performance.
To start the journey of bringing in the remote dark data, MPLX collaborated with Monaco, an OSIsoft OEM who has embedded OSIsoft Message Format (OMF) into its MCore Secure Data Router (MCore SDR). MCore SDR is an industrially hardened multiprocessor, multiprotocol device used to connect edge devices. The MCore SDR uses industrial security to efficiently connect to the PI System. The edge device can also perform edge analytics such as running the ACI compressor modeling software.
MPLX started with 150 of its 850 remote compressors, each with approximately 250 data streams. It developed a number of Asset Framework (AF) templates to address common and unique compressor-related components. It also developed unique anomaly detection analysis templates that were deployed in more than 3,000 instances. With an asset data model in place in AF, it was able to configure web-based PI Vision displays to visualize performance across its compression fleet.
Another key feature that significantly decreased the setup time for a new compressor was the use of OMF's capability to create the AF structure and auto create the 250 PI tags for each of the compressor's data streams. This also drove standardization and ease of use.
The results have been a marked increase in reliability and availability with a corresponding decrease in associated O&M costs. Today, the compressor fleet's subject-matter experts (SMEs) can efficiently provide exception-based remote support to the frontline personnel while working from home.
MPLX will continue rolling to the next round of 150 remote compressors in 2021 on its way to having all 850 remote compressors being monitored in the PI System to optimize their performance.
Figure 1: Topology of the MPLX remote compressor connectivity and data flow