EIT Manufacturing on Paving the Way for Future Proof Industry in Europe
Add bookmark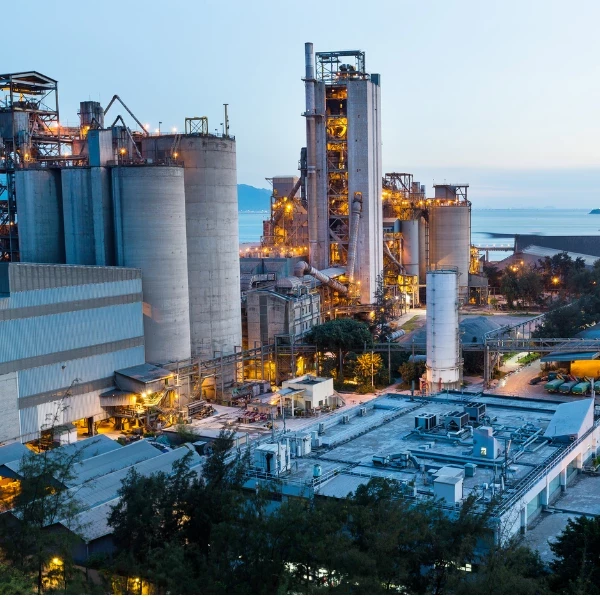
Manufacturing, the backbone of the European economy and the main driver of industrial innovation, job creation and growth, is currently navigating the Fourth Industrial Revolution, or “Industry 4.0”, an age marked by automation and connectivity. The strive to retain leadership status in a competitive global landscape, while going through an industrial transformation is a feat the industry hopes to achieve with accelerated innovation and directed investments.
Within the roadmap designed to ensure competitiveness and sustainability lies EIT Manufacturing, a public-private partnership co-founded by the European Union. Established in 2019, EIT Manufacturing operates with the purpose to improve people's lives through sustainable manufacturing, accompanied by a mission to connect manufacturing players by promoting talent and entrepreneurship to accelerate sustainable innovation in Europe.
The partnership aims to help Europe meet ambitious climate goals and address the growing skills and talent gap faced by the industry in light of an ageing population EIT Manufacturing is addressing those two challenges through their innovation and education efforts, shares Caroline Viarouge, Chief Executive Officer at EIT Manufacturing. Caroline joins us ahead of her keynote panel at The Connected Worker Europe Summit, taking place in Munich, Germany, from 4-6 December.
In this interview, Caroline shares her insights on the role of Connected Worker in the industry 5.0 operating environment and what EIT Manufacturing is doing to upskill the current workforce and attract the right talent to the manufacturing sector while ensuring Europe keeps its competitive edge.
Maryam Irfan, Oil and Gas IQ: Can you tell us a bit about EIT Manufacturing's vision and what have been the challenges and successes so far?
Caroline Viarouge: At EIT Manufacturing, we have had to rethink our vision following the different challenges and crises we've encountered in the last few years.
Firstly, the COVID-19 crisis highlighted the vulnerabilities of our complex global supply chain, followed by the Ukrainian war in recent years, which underscored the challenges we face in energy management, and more recently, the inflationary challenge.
Another challenge we are addressing is the aging population and the talent and skills gap we see in Europe, specifically in the manufacturing sector. Additionally, we’re navigating the climate situation and its impact on greenhouse gas emissions in manufacturing, something particularly close to our hearts.
Given these challenges, we at EIT Manufacturing are diligently rethinking our vision statement.
To answer your question about the positive outcomes, we have seen promising progress. In the past two years, we have seen notable developments in EU policies. The introduction of the AI Act has provided a regulatory framework to guide the emergence of new technological and deep-tech activities. We've also witnessed increased discussions around the Net Zero Industry Act, signalling a greater commitment to a greener industry. Plus, the Critical Raw Materials Act aims to secure the resilience of strategically important materials in the European value chain. We are also fully supportive of the Green Industrial Plan looking ahead to climate neutrality.
At the national level, several Member States are making substantial investments to bolster their resilience and sovereignty in manufacturing. For instance, France has committed over €30 billion towards the manufacturing sector, healthcare, the ecological transition, and transport, with the objective of to make the country one of the most innovative in Europe. Similar investments are occurring in other European countries. It's encouraging to see both Member States and European institutions taking steps in the right direction and allocating resources accordingly.
That said, in certain aspects, progress has been slow, particularly in addressing environmental concerns. There is a pressing need for more robust regulations to compel industries to engage in this transformative journey, encompassing both digital and environmental aspects. It is only by reinforcing regulations that we can hope to move the needle. So, while we’ve seen progress, there is still much work to be done.
READ: Implementing Connected Worker at Duravant
Maryam Irfan, Oil and Gas IQ: You spoke of the ageing population and the skill gap as one of the major challenges in the industry. What is EIT Manufacturing doing to upskill the current workforce and attract the right talent to the manufacturing sector?
Caroline Viarouge: We are actively addressing this issue. From an attraction standpoint, EIT Manufacturing is collaborating with ten universities across Europe to develop and offer master's and doctoral programs in the manufacturing space. Additionally, we are introducing innovation and entrepreneurship programs as part of our summer and winter schools, all of which have received high acclaim. This is to equip the market with both competence and talent, along with a forward-thinking approach to the possibilities that manufacturing and entrepreneurial spirit can bring to the field.
Another critical aspect we’re focusing on is what we call "lifelong learning". For us, this entails reskilling and upskilling the existing workforce within the human capital pool. To facilitate this, we have developed content through the Skills.move Learning Platform and we work closely with industrial partners to customize and create specific training paths to help upskill and reskill their workforce, ensuring the smooth operational transition.
Another noteworthy initiative led by the EIT community and coordinated by EIT Manufacturing is the "Deep Tech Talent Initiative". Recognizing the need for skilled professionals to leverage new technologies and drive the green and digital transition, the European Commission launched this program, with EIT Manufacturing playing a pivotal role in its delivery. The Deep Tech Talent Initiative is a pioneering program aimed at upskilling one million people in the deep tech field within Europe over the next three years. Currently, there are 624,880 pledged talent by 32 Pledgers with 51 courses readily available on the Deep Tech Initiative website. This initiative represents a substantial step forward in bridging the skills gap and preparing for the challenges and opportunities that deep tech knowledge will bring.
Maryam Irfan, Oil and Gas IQ: What role do you see for connected worker technologies in the industry 5.0 operating environment?
Caroline Viarouge: The role connected technology will play is of extreme importance, especially as we talk about human-centricity and the interaction between humans and machines.
If we consider the three primary roles it will play, the first is collaboration and interaction. The Connected Worker will enable seamless communication and collaboration between humans and machine intelligence. This will result in time and cost savings, as well as improved efficiency of machinery. It allows workers to receive real-time information, leading to quicker reactions and more efficient collaboration between humans and machines. This collaborative approach ultimately leads to higher productivity and effective utilization of resources.
The second aspect is skill enhancement and training. Here the Connected Worker can facilitate continuous skills development and training through augmented or virtual reality. Workers can be trained in advance for specific tasks, and real-time guidance can improve the learning curve and the accuracy of complex procedures. This can significantly reduce the learning curve and enhance performance.
The third aspect, particularly in operational and manufacturing spaces, is the safety of the workers. Safety is a top concern in our industry, and Connected Worker technology can monitor working conditions and provide alerts in hazardous situations. In high-risk activities or breaches of safety protocols, machines can detect the risks and contribute to our goal of achieving zero accidents and incidents in the workplace.
LISTEN: Building a Global Culture of Continuous Improvement
Maryam Irfan, Oil and Gas IQ: How easy is it to implement these technologies?
Caroline Viarouge: Successful implementation comes with an overarching digital strategy and a well-defined set of activities. It can be challenging for organizations to begin, especially in manufacturing with multiple sites. The most important thing is to start by understanding the potential benefits and successes that digital transformation can lead to.
One needs to be resilient in navigating the various stages of digitization as the rewards are huge, spanning across productivity, quality, safety, innovation and even extending to product design and implementation. The sky is the limit!
While the pathway is not easy and requires careful planning, persistence from management, and team commitment, the potential rewards make it a journey worth undertaking.
Maryam Irfan, Oil and Gas IQ: Can you tell us about your Green Manufacturing Accelerator program and how you plan to bring the circular economy and Industry 5.0 vision to life?
Caroline Viarouge: Green manufacturing is a significant strategic objective for us at EIT Manufacturing. As we talk about the idea of European reindustrialization, our commitment to Green Manufacturing is to do it right, with a strong emphasis on environmental sustainability.
The Accelerator Program plays a pivotal role within our efforts. We select startups operating in the green technology sector to participate in an intensive three-month program. During this time, we offer a range of workshops and coaching sessions tailored to the unique needs of green product development. We cover topics including business modeling, impact analysis, and product design with a focus on sustainability, and we provide guidance on how to refine and expand green product offerings in the market.
Additionally, participants gain access to the extensive network and support offered by EIT Manufacturing. This program has been successfully conducted in the past, and we are committed to continuing in the same vein with a specific emphasis on fostering the growth of early-stage startups in the green manufacturing sector. Our goal is to help promising startups progress to the next level in their development journey.
The last program only finished in June this year, so it is quite early to talk about success at this stage, but we can’t wait to see what the programme achieves.
READ: Enpro’s Journey towards Human Driven Digital Transformation
Maryam Irfan, Oil and Gas IQ: What are you most looking forward to at this year’s Connected Worker Europe conference?
Caroline Viarouge: I'm very excited about this event because I believe we're all facing critical challenges in European manufacturing, particularly the twin transformation both digital and green manufacturing. I’m eagerly looking forward to engaging with participants from various sectors, industries, and functions to gain insights and understand how we can collectively support this transition.
Ultimately, it is all about partnership and collaboration and we’ll only achieve our goals if we foster cooperation across the entire industry.
Interested in learning more about this topic?
Caroline Viarouge, Chief Executive Officer at EIT Manufacturing, will be presenting her approach at The Connected Worker, Europe Summit this December. If you want to understand how to better connect your workforce to the digital resources they need to work more effectively and increase productivity across your manufacturing operations, then our Connected Worker Europe Summit is your must attend event of 2023.
Join over 150 of your peers in Munich to discuss what’s next for Connected Worker in the Manufacturing 4.0 Operating Environment and learn to develop a holistic ecosystem of connected people, connected processes, connected technologies, and connected data. Download the agenda for more information.