A Guide to FPSO: Floating Production Storage and Offloading
Understanding a core element of the oil & gas extraction and refinement process.
Add bookmark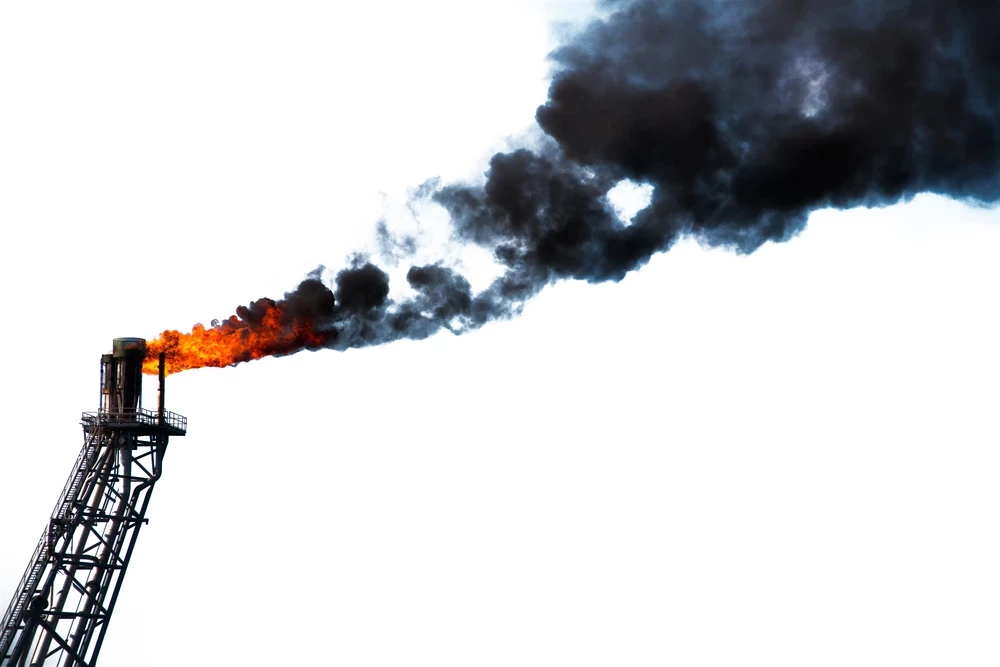
What is FPSO?
At its core, an FPSO facilitates the processing and storage of oil and gas at sea.
It stands for floating production storage and offloading (FPSO). These vessels are used extensively by the offshore industry and have become one of the primary methods of oil and gas processing and storage. As its name suggests, an FPSO is a floating vessel that acts as a mobile offshore production and storage facility. They are typically employed and leased by oil and gas companies.
The vessels themselves are equipped with processing equipment for the separation, storage and offloading of oil and gas that comes from sub-sea oil wells or platforms. When oil and gas is processed, it is safely stored in the FPSO until it can be offloaded onto a tanker or a pipeline for transportation ashore.
Origins of FPSO
The first FPSO was a converted oil tanker, built by Shell in 1977. Before the time of FPSOs, oil and gas extraction was more difficult and inefficient. Companies were only able to extract oil and gas from shallow fields, no more than a water depth of 50 metres. Oil and gas had to be transported to land via a subsea pipeline, which is economically unviable at water depths more than several hundred metres and in instances where the seabed oil and gas fields are hundreds of miles away from the shore.
READ: An Introduction to the Oil and Gas Industry
Oil and gas awaiting transport was stored in tankers called floating storage and offload units (FSO). FSOs were used to store extracted hydrocarbons (a mixture of oil, gas and water) and transport it from remote locations such as distant seabeds. However, FSOs can’t process oil and gas, which is where the FPSO comes in.
What is FPSO?
As onshore oil discoveries continue to decline, FPSOs will become increasingly more vital for the oil and gas industry. There are more than 200 FPSOs today operating around the globe. They're less expensive than traditional offshore oil and gas platforms, more flexible, safer, and time-efficient. Here is a breakdown of the FPSO acronym:
- Production – The “P” in FPSO is what separates these vessels from FSOs. Production refers to the processing of oil and gas. Hydrocarbons are produced in seabed wells and this is transported to the FPSO via flowlines and risers. The hydrocarbons are then separated into oil, gas, water and impurities via the production facilities on the deck of the FPSO.
- Flowlines – Flowlines carry hydrocarbons directly from seabed well. These can be flexible or rigid.
- Risers – Developed for vertical transportation. This is the section of the line from the seabed to the topside.
- Storage – Once the oil has been processed, it is transferred to cargo tanks in the double hull of the vessel.
- Offloading – Offloading refers to transferring the gathered contents to additional transfer conduits. Crude oil that is stored in the vessel is then transferred to tankers and pipelines heading ashore. Gas is either transported to the shore via pipeline or recycled back into the field to increase production.
FPSO Design
In terms of design, most FPSOs take the form of a supertanker and it can be difficult to distinguish between the two. The defining visual difference of an FPSO is the processing equipment that is stored aboard the vessel’s deck. Meanwhile, hydrocarbon storage facilities are typically situated below the hull.
READ: Guide to shutdowns and turnarounds
Traditional tankers can be converted to an FPSO, giving them an additional element of flexibility. In terms of mooring, the FPSO vessels can be anchored to multiple points on the sea floor, which is called spread morning, or via a central weather vane.
In addition to oil and gas processing equipment, FPSOs can be expected to have living quarters to provide accommodation for staff during long periods out at sea, along with control rooms, offices and recreational facilities.
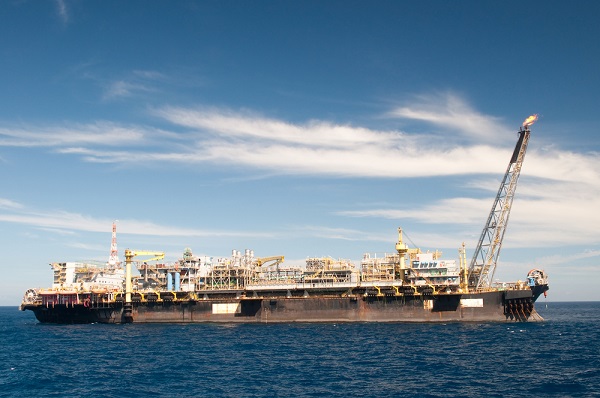
Here is a rundown of the core components of an FPSO vessel.
- Spread mooring: Spread mooring is a traditional mooring system, incorporating a number of mooring lines attached to the hull of the vessel. These mooring lines are anchored onto the seabed.
- FPSO turret (weathervaning) – The turret is integrated into the FPSOs hull, so the hull weathervanes around the mooring system and the mooring line. This enables FPSOs to position the vessel favourably against the wind so that it remains bow to wind and weather.
A turret mooring system is critical for harsh weather conditions. In essence, the turret enables the FPSO to freely rotate while moored to various locations on the seafloor. - Detachable FPSO turret - Many turret systems allow the turret to be disconnected from the vessel, but remain attached to the mooring lines on the seabed. This is particularly useful in situations such as hurricanes and storms, where the vessel needs to react quickly to external hazards. Once the threat has been mitigated, the FPSO can return to the turret, reattach and continue operations. This mooring system is by far the most flexible.
- Gas dehydration – Gas is often saturated with water vapour, which poses a threat to facilities. Gas dehydration removes the water that is associated with natural gas.
- Gas compression – Natural gas must be treated to conform to commercial standards.
- Water injection – Water injection is a process where water is introduced into a reservoir to encourage oil production.
- Gas, water and oil separator – As water, gas and oil have different densities, they can be separated with gas rising to the top, water on the bottom and oil staying in the middle. Additional debris such as sand will settle at the bottom.
- Seawater treatment – Sea water treatment involves removing sulfates and other unwanted elements from injection water.
Benefits of FPSO
Why have FPSOs become so important for oil & gas companies?
Conceptually, FPSOs have given oil and gas companies a lot of freedom and versatility with regards to exploration and extraction. FPSOs enables companies to produce oil & gas and explore increasingly remote areas at a cheaper price in comparison to traditional offshore oil and gas production and storage methods.
FPSOs have six key advantages.
- Time – FPSOs can connect to any pipeline. In addition, when an existing oilfield is depleted, an FPSO can move to another location. This saves time and money and mitigates the need to build expensive permanent pipelines and facilities. As such, FPSOs make an ideal solution for smaller oil and gas fields that will be depleted in a matter of years.
- Cost – With FPSO, O&G companies are not required to build permanent structures like pipelines and piled buildings. FPSOs have the capability to store processed oil and gas and offload it to shuttle tankers for transportation to refineries.
According to Investopedia, a purpose-built FPSO can cost north of $800 million, especially if their production capabilities exceed 250,000 barrels per day (BPD). Meanwhile, a traditional offshore oil platform can cost up to $650 million. While the initial cost of an FPSO is slightly higher, FPSOs prove to be more cost-effective in the long run.
The cost of a traditional offshore oil platform can skyrocket when other expenditures are taken into account, such as maintenance, well completion costs and platform decommissioning costs. - Safety – FPSOs can be disconnected from the pipelines and oil wells they are moored to. This makes FPSOs a safer option in areas with severe weather conditions.
- Convenience – Oil producers can lease the vessels, giving oil and gas companies greater flexibility over their assets ensuring they can react to market forces. An oil and gas producer can conceivably lease as many or as little FPSOs as they want. This kind of flexibility isn't feasible with fixed assets which take years to build and finance. This not only saves costs but it bridges the gap between small and large oil and gas organisations, ensuring healthier competition.
- More viable fields - Some oil and gas fields lack commercial viability due to weather hazards, the distance to the shore or the cost-inefficiency of building and maintaining traditional infrastructure. FPSOs mitigate this by being insensitive to deep-water and adverse weather.
- Storage capabilities – FPSOs can store a substantial amount of oil and gas, increasing the commercial viability of hard to reach fields.
Limitations of FPSO
While there are numerous advantages to FPSO, it does have a few limitations.
- Conversion time – Converting a tanker into an FPSO can take up to two years. While this is something to consider, it is still substantially faster than building a pipeline.
- Self-competition – Companies may find that they are competing with their own pipeline-based infrastructure.
- Initial Cost – The upfront cost of an FPSO can be more than the cost of building a large fixed offshore platform.
Related systems: Types of floating storage unit
There are a wide array of offshore vessels and design variants of the FPSO. Here is a rundown of the most popular deviations.
- Floating production systems (FPS) – FPS is an umbrella term for all variants of floating production systems, including vessels and platforms
- Floating storage and offloading (FSO) – An FSO is a simplified version of an FPSO. It has the capability to store and offload oil and gas but it doesn’t possess the ability to process it.
- Floating storage units (FSU) – Floating storage units to take the form of a large barge in contrast to supertankers that are associated with FPSOs. Simply put, these units are used to store oil and gas in large silos placed on top of the vessel.
- Floating drilling production storage and offloading (FDPSO) – This variant is still relatively new, with the first of its kind setting sail in 2009. The key difference with this vessel is the modular drill that is attached to the hull of the ship, giving it more utility than a standard FPSO. With the addition of a drill, an FDPSO can perform nearly all major functions associated with offshore oil and gas production.
- Floating liquid natural gas vessel (FLNG) – A FLNG is a type of vessel that is more gas-centric. It has all of the apparatus to enable offshore liquidification of natural gas into liquefied natural gas (LNG).
Digitization: the future of FPSO
Like many other sectors, oil and gas is experiencing the steady digitization of operational procedures to promote efficiency and save costs. However, unlike other industries, oil and gas has been slow to adopt increased connectivity and the technologies associated with the Internet of Things (IoT).
The rapid conversion of operational technology (OT) and information technology (IT) has resulted in increased efficiency through big data, analytics, sensors, the ability to automate highly sensitive tasks and more.
Going forward, FPSOs will likely have to incorporate more digitisation. From fleet data to analytics tools and predictive analytics, these technologies can be used to determine success rates, estimations of topside components and more.
Monitoring technologies are far better now than they were many decades ago when most FPSOs were commissioned. The digitization of FSPO has helped prolong the shelf life of many older vessels. Companies now have a better grasp measuring the fatigue of vessels and how each project impacts a vessels service life. Organisation now has data on hulls, mooring systems, processing equipment and everything in between.
Not only does this lead to intact components of a vessel being recycled, but the data produced also leads to more efficient designs.
READ: Harnessing Gen AI for Workflow and Maintenance Optimization
Join senior operations, digital, data and AI leaders from oil and gas, utilities, and more at our upcoming events:
Connected Worker: Energy Summit
March 18-20, 2025 | Houston, TX
AI in Energy Summit
February 24-25, 2025 | Houston, TX