The First Benefit of Damage Mechanism Reviews
Damage (corrosion) mechanism reviews in achieving regulatory compliance with several OSHA standards in the United States.
Add bookmark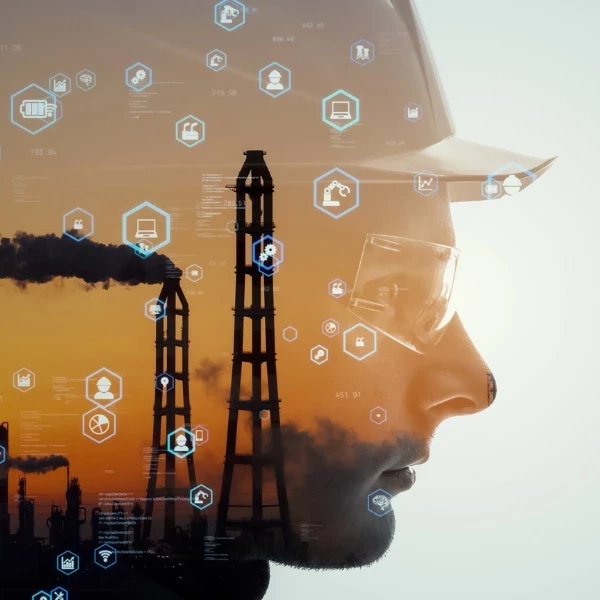
Contributed by: Dheerajkumar R Narang
The landscape of regulatory compliance with OSHA standards in the United States is ever-changing and complex. The effectiveness of regulatory compliance with OSHA standards relies heavily on advanced and multi-disciplinary engineering assessments, and one such engineering assessment that pertains to achieving successful compliance is damage (corrosion) mechanism reviews. The damage (corrosion) mechanism reviews are always the first step in designing pressure-containing or structural equipment or other types of asset for which compliance is sought with an applicable OSHA standard. This technical article will describe the importance of damage (corrosion) mechanism reviews in achieving regulatory compliance with several OSHA standards in the United States. The article also builds on the previously published [1] scientific methodology on the usefulness of damage mechanism reviews for both process safety management and asset integrity (reliability) management for process plant industries in the United States. The first benefit of DMRs is that it helps achieve compliance with all the engineering-intensive PSM elements with significant efficiency improvement and cost savings.
Damage Mechanism Review(s) Process
Damage mechanism [1], in the process industry, is defined as a degradation phenomenon for all types of equipment, structure and process piping that may occur during manufacturing, operation, repair and upset conditions. Degradation of the pressure equipment and process piping can be mechanical, thermal, metallurgical, environmental cracking or thinning. Degradation depends on the specific grade of metallurgy, operating conditions, design and construction code, shape and size of the equipment and piping, process fluid constituents etc. Therefore, damage mechanism review is often the first step for the above mentioned PSM elements compliance and numerous other reliability or asset integrity engineering assessments for the plant assets. Primarily, the loss of containment and production rate scenarios arising out of pressure equipment (static and rotary) and process piping failures are addressed in a variety of engineering and optimization assessments with damage mechanism identification being the first and foremost step. Note that, facilities that are not explicitly covered by the federal or state process safety management (PSM) regulations also rely on damage mechanism reviews (DMR) for their mechanical integrity, inspection, and reliability management programs.
The DMR process [1] can be defined as an engineering assessment that systematically and methodically determines the susceptible and credible damage mechanisms and their most probable failure modes for in-service pressure equipment or piping system constructed with a specified construction code and metallurgy, operating under specified operating conditions with a specified process fluid composition. Note that design and construction aspects of pressure equipment also play a crucial role in identifying mechanical or metallurgical defects that may arise from a specific manufacturing and welding process and subsequently propagating into a failure mode during operation.
READ: Developing a Comprehensive OT Cyber Security Strategy for Manufacturing Sites
DMR process [1] identifies the following type of damage mechanisms:
- Mechanical or operational damage mechanisms such as mechanical fatigue and vibration fatigue
- Metallurgical damage mechanisms such as 885°F and sigma phase embrittlement
- Environmental thinning damage such as sulfidation, naphthenic and carbonic acid corrosion
- Environmental cracking damage such as chloride and carbonate stress corrosion cracking
- Damage mechanism due to combined effect of environment, operation, and inherent manufacturing defects. Example, dissimilar weld metal cracking and brittle fracture
A DMR team [1] typically comprises of the following personnel at a facility:
- Unit team leader and facilitator for the damage mechanism review assessment
- Unit operator to provide inputs on process control techniques, operating windows, history of incidents and emergency response options
- Unit inspector to provide inputs on extent of damage observed in the field, equipment inspection, maintenance, and repair history
- Unit or area mechanical integrity or reliability engineer to provide inputs on equipment design, past repairs and re-rates, equipment availability targets
- Unit or area materials & corrosion engineer to provide inputs on susceptibility of damage mechanism in variety of process environments, and feasibility of integrity operating window
- Cross-functional team member from other PSM elements such as PHA facilitator or PSI focal point for a specific process unit or area
The generic DMR process for process safety management (PSM) compliance is depicted in Figure 1 and covered in the technical article.
Figure 1. Damage Mechanism Review (DMR) Process [1]
Damage mechanism reviews (DMR) [1] also have significant importance in the design and construction stage of a process plant facility be it covered under PSM regulation or not. Since the material selection and verification activities undertaken by the front-end engineering design (FEED) and engineering, procurement, and construction (EPC) contractors are heavily dependent on the identification of mechanical, metallurgical, and environmental damage mechanisms for the pressure equipment, process piping and other process containment assets.
READ: Sustainable Operational Excellence in a Shifting Landscape
This technical article will describe the first benefit of conducting site or unit wide damage mechanism reviews. The first benefit [1] of DMRs is that it helps achieve compliance with all the engineering intensive PSM elements with significant efficiency improvement and cost savings. Second benefit of DMRs is that it leads to cost effective and efficient implementation of major reliability (asset integrity) best practices such as robust inspection program (IP), integrity operating windows (IOWs) and risk driven asset reliability plans (ARPs), bad actor management (BAM) program and performing fitness for service (FFS) assessments. The third benefit is that it helps process plant facilities in achieving regulatory compliance with several federal OSHA regulations in the United States other than the process safety management.
The second and third benefit of DMRs will be explained in the subsequent articles of this series.
Federal and State Process Safety Management Regulations
The Process Safety Management (PSM) of Highly Hazardous Chemicals Regulation was issued in February 1992 under 29 CFR 1910.119. PSM regulations primarily apply to hazardous and flammable processes rather than specific types of plants or facilities. Although, the exclusion of certain types of facilities are explicitly stated in the federal OSHA PSM regulation [1,2].
OSHA PSM does not cover oil and gas drilling facilities, nuclear energy, federal water treatment, retail, normally unoccupied remote, and transportation facilities. The following are the 14 elements of OSHA PSM standard listed in the code of federal regulation register 29 CFR 1910 [1,2].
- 29 CFR 1910.119(c) - Employee participation (EP)
- 29 CFR 1910.119(d) - Process Safety Information (PSI)
- 29 CFR 1910.119(e) - Process Hazards Analysis (PHA)
- 29 CFR 1910.119(f) - Operating Procedures (OP)
- 29 CFR 1910.119(g) - Training (TNG)
- 29 CFR 1910.119(h) - Contractor (CON)
- 29 CFR 1910.119(I) - Pre-Startup Safety Review (PSSR)
- 29 CFR 1910.119(j) - Mechanical Integrity (MI)
- 29 CFR 1910.119(k) - Hot Work Permit (HWP)
- 29 CFR 1910.119(l) - Management of Change (MOC)
- 29 CFR 1910.119(m) - Incident Investigation (II)
- 29 CFR 1910.119(n) - Emergency Planning and Response (EPR)
- 29 CFR 1910.119(o) - Compliance Audit (CA)
- 29 CFR 1910.119(p) - Trade Secret (TS)
OSHA also allows states to develop, manage and enforce their own approved process safety management programs. New Jersey, California, Delaware, and Washington states had developed their own process safety management programs in the past and got these approved by the federal agency OSHA before or around the same time OSHA PSM regulations were originally promulgated in the year 1992 [3,4]. Some of the federal OSHA approved state process safety management (PSM) regulations are tabulated in Table 1.
Table 1. Federal OSHA Approved State Process Safety Management Regulation(s) [5–8]
Process plant facilities [1] covered under the above federal and state PSM programs are required to comply with all its requirements categorized in the form of regulatory elements. There are numerous engineering frameworks, methodologies, and software available in the industry to conduct PSM assessments, and generate documentation required to demonstrate compliance. All the PSM elements are interlinked with one another, but the following OSHA PSM elements [1] require intensive or detailed engineering assessments.
- Process Hazard Analysis
- Process Safety Information
- Mechanical Integrity
- Incident Investigation
Process Safety Management (PSM) Compliance Regulatory Changes
OSHA is currently in the process of a major rulemaking effort leading to significant changes to the federal process safety management (PSM) regulations. The 2013 ammonium nitrate explosion in a Texas facility [9] led process industry and federal government focus their attention on the shortcomings in the federal PSM standard and ever since the federal agency (OSHA) has been working on revising the OSHA PSM standard through a rulemaking initiative under federal docket OSHA-2013-0020 [10,11].
The proposed revisions to key PSM elements in the new federal OSHA PSM standard are following [10–14]:
- Addition of recognized and generally accepted as good engineering practices (RAGAGEP) and critical equipment definitions to the subsection (b)
- Improve employee participation, stop work authority to subsection (c)
- RAGAGEP updates and consequent changes to be evaluated and incorporated in process safety information to subsection (d)
- Justification and documentation for PHA recommendations not implemented, safer technology and alternative analysis, addition of natural disasters and extreme temperatures scenarios in process hazard analysis to subsection (e)
- Extension of mechanical integrity coverage to all critical equipment, clarification on the definition of equipment deficiencies to subsection (j)
- Add management of change requirement for organizational changes in subsection (l)
- Root cause failure analysis requirement addition to subsection (m)
- Field coordination with local emergency responders to subsection (n)
- Compulsory third-party compliance audits, development of facility PSM standard that mandates periodic review and updating including written procedures for all the PSM elements to subsection (o)
OSHA is yet to conclude the PSM rulemaking proposed under federal docket OSHA-2013-0020, and these changes are not incorporated as of June 2024.
READ: Case Study: Understanding SLB’s 'Living Our Culture' Program
California and Washington states have incorporated major changes to their state PSM regulations especially for the petroleum refineries in the recent past. California promulgated a new PSM standard under Title 8, Section 5189.1 applicable to petroleum refineries in the year 2016. Note that this new PSM standard does not apply to chemical facilities in California, and these are still covered under the old California PSM standard Title 8, Section 5189 [5,15]. Washington state has also adopted a similar approach and promulgated a new PSM standard for petroleum refineries under WAC 296-67-300 effective from December 2024 with the old WAC 296-67-001 being applicable to chemical facilities, which remained unchanged [6,16].
The following are the summary of changes in the new California and Washington state PSM standards for petroleum refineries [5,6,15,16]:
- PSM program stewardship requirement where written plan of employee collaboration throughout all aspects of PSM implementation. Refinery manager designated with sign off authority and responsible person for PSM compliance
- Damage mechanism reviews (DMRs) for all existing and new covered processes with necessary documentation stating reasons if and where a damage mechanism identification and review does not exist
- Multi-layer or hierarchical hazard controls analysis (HCAs) requirement every five years
- Process hazard analysis (PHA) requiring incorporation of DMRs and HCAs results
- Assessment of human factors in operating and maintenance procedures at facilities. Human factors programs (HFP) include organizational changes, environmental compliance, and individual physical factors such as fatigue or mental health issues
- Management of change process to include organizational change scenarios
- Root cause failure analysis requirement including both initiating and underlying causes. Reviewing HCA, DMR and PHA reports. Identification of management system failures due to organizational and safety culture shortcomings
- Process safety culture assessment requirement every five years
Process Safety Management (PSM) Compliance and Damage Mechanism Review(s)
Table 2 below highlights how the DMR as an explicit or implicit regulatory requirement interacts with other PSM elements [1].
Table 2. Interaction Matrix of DMR Process with other PSM Element(s) [1]
Note that the PSM elements HCA and RCA are additional elements recently promulgated in Cal OSHA and Washington state PSM program [5,16]. It is evident from Table 2 that perfecting DMR process will lead to improved cost efficiency and procedural effectiveness in the overall PSM compliance effort at a facility.
The Federal PSM standard anticipates a clear definition of the term equipment deficiencies in future revision, and the clarity may include assessing all types of damage mechanisms and failure modes that critical equipment may experience at a PSM facility [11,14]. Though Federal OSHA PSM standard revisions do not include adding a standalone damage mechanism review element, the above Table 2 clarifies that adopting a DMR centered PSM compliance process is in the best interest of a PSM facility, primarily for pressure equipment with a potential for loss of containment or production scenarios [11].
Thus, the first benefit [1] of the DMR process is that it helps achieve compliance with all the engineering intensive PSM elements with significant efficiency improvement and cost savings. It is essential to streamline the resource and cost estimation process by considering the above-mentioned interaction between DMR process and other federal and state PSM standard elements.
Conclusion
This technical article discussed the first benefit of conducting site or unit wide damage mechanism reviews. The first benefit of DMRs is that it helps achieve compliance with the engineering intensive PSM elements with significant efficiency improvement and cost savings. A five step DMR process [1] for process safety management compliance was explained along with interactions of DMR process with other relevant PSM elements. Recent regulatory changes in the federal and state PSM standards, focusing on damage mechanism review were also described.
Second benefit [1] of DMRs is that it leads to cost effective and efficient implementation of key reliability (asset integrity) best practices such as robust inspection program (IP), integrity operating windows (IOWs) and risk driven asset reliability plans (ARPs), bad actor management (BAM) program and performing fitness for service (FFS) assessments. The third benefit is that it helps process plant facilities in achieving regulatory compliance with several federal OSHA regulations in the United States other than the process safety management.
The second and third benefit of DMRs will be explained in the subsequent articles of this series.
LISTEN: Episode 11: Avoided Methane Emissions Into Revenue: Gas-to-Value Explained
Abbreviations and Definitions
- AMPP: The Association for Materials Protection and Performance
- API: American Petroleum Institute
- API RP: American Petroleum Institute Recommended Practice
- ARP: Asset Reliability Plan
- ASME: American Society of Mechanical Engineering
- BAM: Bad Actor Management
- CA: Compliance Audit
- CAD: Computer Aided Design
- CCD: Corrosion Control Document
- CFR: Code of Federal Regulation
- CLD: Corrosion Loop Diagram
- CMD: Corrosion and Material Diagram
- CMP: Corrosion Management Program
- CON: Contractor
- DMR: Damage Mechanism Review
- EP: Employee Participation
- EPA: Environmental Protection Agency
- EPC: Engineering Procurement Construction
- EPR: Emergency Planning and Response
- ER: Electrical Resistance
- FEED: Front End Engineering Design
- FFS: Fitness for Service
- FMECA: Failure Mode Effects and Criticality Assessment
- HCA: Hazard Control Analysis
- HFP: Human Factor Program
- HWP: Hot Work Permit
- IBR: Indian Boiler Regulation
- II: Incident Investigation
- IOW: Integrity Operating Windows
- IP: Inspection Planning
- LPR: Linear Polarization Resistance
- MI: Mechanical Integrity
- MOC: Management of Change
- MTBF: Mean Time Between Failure
- MTTF: Mean Time to Failure
- NACE: National Association of Corrosion Engineers
- NJAC: New Jersey Administrative Code
- OP: Operating Procedures
- OSHA: Occupational Safety and Health Administration
- PFD: Process Flow Diagram
- PHA: Process Hazard Analysis
- PID: Piping and Instrumentation Diagram
- PSI: Process Safety Information
- PSM: Process Safety Management
- PSSR: Pre-Start Up Safety Review
- RAGAGEP: Recognized and Generally Accepted Good Engineering Practice
- RBI: Risk Based Inspection
- RCA: Root Cause Analysis
- RCM: Reliability Centered Maintenance
- RMP: Risk Management Program
- RMS: Reliability Management System
- TNG: Training
- TS: Trade Secrets
- WAC: Washington Administrative Code
References
Narang D. Dual Benefits of Damage Mechanism Reviews. In: 2024 Spring Meeting and 20th Global Congress on Process Safety. AiCHE; 2024. Accessed June 2, 2024. https://www.aiche.org/academy/conferences/aiche-spring-meeting-and-global-congress-on-process-safety/2024/proceeding/paper/83c-dual-benefits-damage-mechanism-reviews
29 CFR 1910.119 -- Process Safety Management of Highly Hazardous Chemicals.; 1992. Accessed December 29, 2023. https://www.ecfr.gov/current/title-29/part-1910/section-1910.119
US EPA O. 1990 Clean Air Act Amendment Summary. Published May 29, 2015. Accessed December 29, 2023. https://www.epa.gov/clean-air-act-overview/1990-clean-air-act-amendment-summary
Summary of the Final Regulatory Impact and Regulatory Flexibility Analysis of the Final Standard for Process Safety Management of Highly Hazardous Chemicals.; 1992. https://www.regulations.gov/document/OSHA-S026-2006-0659-0744
5189.1. Process Safety Management for Petroleum Refineries, California. Accessed December 29, 2023. https://www.dir.ca.gov/title8/5189_1.html
Chapter 296-67 WAC Safety Standards for Process Safety Management of Highly Hazardous Chemicals. Accessed January 21, 2024. https://app.leg.wa.gov/wac/default.aspx?cite=296-67
Toxic Catastrophe Prevention Act (TCPA) Program, State of New Jersey. Accessed January 31, 2024. https://www.nj.gov/dep/enforcement/tcpa/tcpadown.htm
1201 Accidental Release Prevention Regulation, State of Delaware. Accessed January 15, 2024. https://regulations.delaware.gov/AdminCode/title7/1000/1200/1201.shtml
CSB INVESTIGATION REPORT ON WEST FERTILIZER COMPANY FIRE AND EXPLOSION, 2013.; 2016. https://www.csb.gov/west-fertilizer-explosion-and-fire-/
Actions to Improve Chemical Facility Safety and Security – A Shared Commitment, Report for the President.; 2014. Accessed December 29, 2023. https://www.osha.gov/sites/default/files/final_chemical_eo_status_report.pdf
Docket OSHA-2013-0020. Unified Agenda and Updates on PSM Rule Making. Published 2013. Accessed December 29, 2023. https://www.regulations.gov/docket/OSHA-2013-0020/unified-agenda
House TW. Executive Order 13990 on Protecting Public Health and the Environment and Restoring Science to Tackle the Climate Crisis. The White House. Published January 21, 2021. Accessed December 29, 2023. https://www.whitehouse.gov/briefing-room/presidential-actions/2021/01/20/executive-order-protecting-public-health-and-environment-and-restoring-science-to-tackle-climate-crisis/
Executive Order 13650 Improving Chemical Facility Safety and Security | whitehouse.gov. Accessed December 29, 2023. https://obamawhitehouse.archives.gov/the-press-office/2013/08/01/executive-order-improving-chemical-facility-safety-and-security
EPA RMP SCCAP Rulemaking Docket EPA-HQ-OLEM-2022-0174. Published 2022. Accessed December 30, 2023. https://www.regulations.gov/docket/EPA-HQ-OLEM-2022-0174/unified-agenda
Wilson M, Hoyle W, Holmstrom D. Protecting Workers from Chemical Catastrophes: California’s 2017 Process Safety Management Regulations for Petroleum Refineries. Accessed January 31, 2024. https://www.ohchr.org/sites/default/files/Documents/Issues/ToxicWaste/Exposure/BlueGreenAlliance.pdf
Washington Adopts New Refinery Process Safety Management (PSM) Rule. Accessed January 21, 2024. https://www.lexology.com/library/detail.aspx?g=2a14b47e-03ad-47be-83ec-3f469e92f2ce