Remote Continuous Improvement: Navigating Covid 19 at Dow Chemical
An interview with Julie Thyne, Global Continuous Improvement Lead at Dow Inc
Add bookmark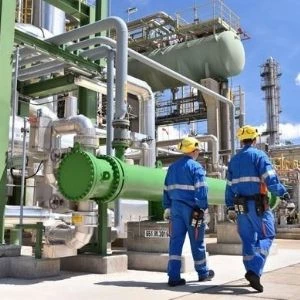
Q: Julie, tell us a little bit about how COVID has impacted Dow’s manufacturing?
At Dow we supply so many products and technologies that support our healthcare, our hygiene and medical industries. We make products for everything, from antiseptics, disinfectants, personal protective equipment, detergents and even memory foam for hospital beds. So, as a result, it’s extremely critical that we keep our plants and our supply chains running. We’re so thankful for our essential workers who are at the plants, conducting their operations safely and productively to keep supplying our customers.
At many of our sites, we’ve implemented some additional safety measures such as temperature monitoring and social distancing during meetings. We have delayed non-essential activities, so we can allow our workers to focus on doing their best work every day.
But, for employees like myself, who can work from home, we’re adjusting to a new normal of conducting our daily work remotely. Our leadership, all the way from the CEO to the frontline managers, have done an amazing job of keeping us all connected through internal websites, daily emails, weekly calls. I’ve been so impressed with our IT organisation, who’s been able to support an exponential increase in remote work, video conferencing and virtual collaboration tool use.
How are you leading Dow’s Continuous Improvement Programme during this time when you and your team cannot physically be in the plant?
I’m pleased to say that Continuous Improvement is going strong at Dow. With our plants operating at reduced staffing levels and so many of us working remotely, there’s never been a greater need for efficient, streamlined operations. The CI team has been engaged to help with numerous projects around the world, including Lean assessments, value-stream mapping and virtual brainstorming sessions.
We’re also quickly working to adapt some of our CI training material for virtual delivery so that we can get just-in-time CI skills and tools into the hands of our engineers quickly.
What technologies are you using to do this continuous improvement virtually?
We’re making use of collaboration tools like Cisco Webex and Microsoft Teams. And while these tools aren’t necessarily new to us, the current situation is inspiring us to find new and creative ways to work together. Webex video conferencing is allowing us to connect with our client partners as well as with each other. Teams is enabling us to easily collaborate on documents and spreadsheets as well as quickly share information with each other.
We also have internal message boards that are monitored by our IT experts and also allow for crowdsourcing. So, if you have a question about one of these collaboration tools, a post to the message board will yield quick responses from both colleagues and IT professionals. Now the CI group is preparing to launch a similar tool for crowdsourcing solutions to CI challenges in our plants.
What would you say you’ve learnt from this experience so far?
I think what I’ve really taken away from this is just the feeling of, our work really matters, this is a great time to remember how important our industry really is and how vital Dow is to the world. We’ve shown that we can rise to any challenge and overcome any obstacle. While this pandemic may be temporary, the work of Team Dow is certainly not. And I think we’re going to come through this with a renewed sense of purpose and the confidence to really deliver big when it counts.