4 Simple Steps to Get Started with Worker/Machine Connectivity Solutions
Add bookmark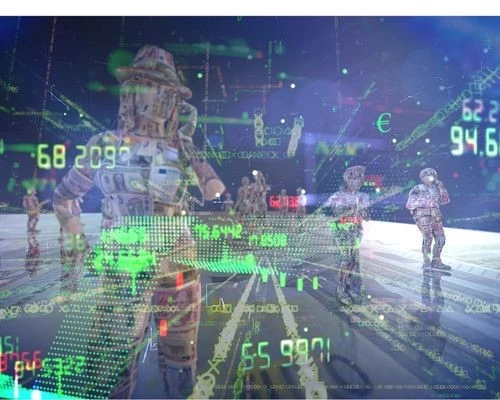
Worker/machine connectivity solutions are key to productivity, efficiency, and enhanced safety in modern oil and gas plants. They offer continuous communication between workers of all skill levels, as well as between workers and machines.
These solutions enable remote real-time process monitoring and an instantaneous exchange of relevant, fresh data that all workers can interact with. They also integrate predictive maintenance processes, which determine upkeep requirements through artificial intelligence and smart software.
Oil and gas companies use worker/machine connectivity solutions to enhance the training of their workers, which helps prevent accidents, human error, and unplanned downtime while enabling optimized production runs and reducing costs.
Worker/machine connectivity solutions are also useful in mining, construction, and manufacturing. According to Polaris Market Research, the global connected worker market had a market size value of $4.21 billion in 2021, and is expected to expand at a compound annual growth rate of 24.2% through 2029.
So, how can you get started with worker/machine connectivity solutions?
Step 1: Build a digital transformation strategy
Worker/machine connectivity solutions require a larger digital transformation approach in order to work efficiently.
Focus on a digital transformation strategy that pre-defines the exact technology you will require and how you will implement it at your workplace.
Al Lindseth, a multiple award-winning Chief Information Officer with 25 years of experience in the energy industry, shares what oil and gas companies usually get wrong about digital transformation:
- They tend to not address the most critical issues first
- They focus on technology deliverables without addressing the behavioral challenges that come with implementing new technology
What’s the point of adding new technology if your workers will not use it?
You need to find what’s best for your company — your employees, specifically — and set up a digital transformation strategy that addresses your plant’s issues from top to bottom, in an organized way.
Step 2: Incorporate the right digital tools
Worker/machine connectivity solutions rely on other digital tools to work properly.
For example, you need to make sure that every worker in your plant has access to at least one mobile device (such as a smartphone or a tablet) so that they can communicate in real time, check the machinery’s status, find digital work instructions, and share knowledge or production updates through specific industrial applications. Wearables, such as smart watches, are also in the “recommended gadget” group because they accelerate training and troubleshooting.
Cloud connectivity is another important factor, as it allows easy, on-demand access to databases. In Industry 4.0, cloud connectivity is gaining priority against physical data centers and servers because of its flexibility, scalability, and reduced costs.
Cloud connectivity also provides a strong disaster recovery plan, as it enables data restoration from remote data centers in minutes. It also increases business value in the energy industry.
To make the most out of your worker/machine connectivity solution, you may also need to integrate enterprise resource planning (ERP) software gradually. ERP software can work with centralized databases that function as a single source of truth for real-time data. Also, it works alongside manufacturing execution systems (MES) to track processes and collect data. This combination simplifies the decision-making process.
Additionally, you should get rid of any legacy apps that do not fit with your new virtual setup.
Step 3: Set a timetable for implementation and deployment
Modern worker/machine connectivity solutions can be deployed in just a few weeks, but you need to know beforehand exactly how much time and resources you can dedicate to the development and implementation of the digital transformation and the worker/machine connectivity solution itself.
For example, if you can’t spend extra money on solid, secure corporate Wi-Fi infrastructure that extends to all the corners of your plant, you may have to install a private LTE network for your connected worker platform to work properly.
Identify the technology involved in your plant’s digital transformation and consider not only how long it will take to deploy, but what it will take to deploy. You will also need to ensure user adoption.
Step 4: Inform your stakeholders
Worker/machine connectivity solutions mainly benefit:
Frontline workers: These solutions simplify their tasks. Less frustrating work leads to higher levels of satisfaction at the workplace, and, as a result, frontline workers become more efficient. This work environment is also naturally more appealing to potential new hires.
Supervisors, managers and directors: Worker/machine connectivity solutions improve process visibility. This way, supervisors, managers and directors can detect and resolve issues more easily. They can make sure that workers follow training materials and evaluate the general performance of the plant — even remotely.
Your business: They boost your plant’s efficiency and productivity, making it therefore more competitive.
Here’s the thing: if your business is on a roll, your stakeholders will be on a roll, too.
The last step of your plant’s digital transformation and implementation of worker/machine connectivity solutions is to let them know about the return on investment (ROI) that the upcoming changes entail.
Spoiler: As the worker/machine connectivity solution increases the workers’ and the plant’s efficiency, ROI goes up as well.
Getting started with worker/machine connectivity solutions is simpler than you think. Follow these four steps to maximize your workforce’s efficiency!
What do you think? Have we missed something? Let us know in the comments below.
Interested in learning more about this topic?
Join us at The Connected Worker Summit on March 28-30, 2023 and network with over 150 of your industry peers at the Norris Conference Center in Houston, TX., and learn how to evaluate the existing gaps in your connected worker capability and identify the data-driven solutions that will drive continuous improvement across your operations. Download the agenda for more information.