Harnessing Gen AI for Smarter Decision-Making and Maintenance Optimization
Lessons in leveraging AI from Partha Chatterjee, Director - Energy, Data and AI at MRE Consulting.
Add bookmark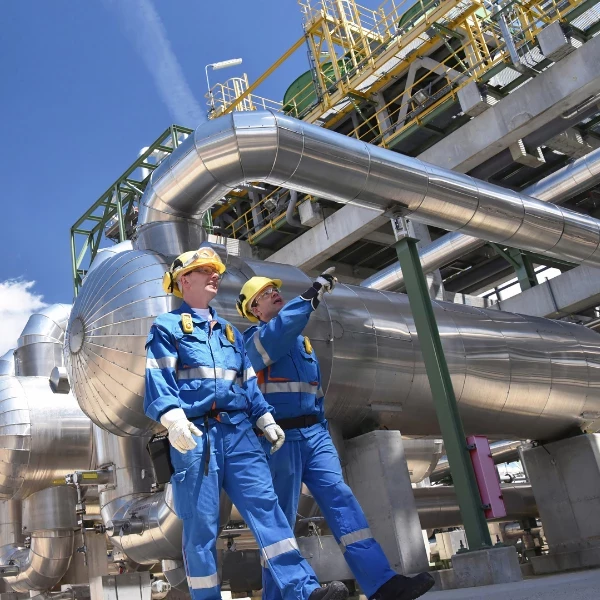
An IBM study stated that about 74% of energy and utility companies globally are either implementing or exploring AI, with the majority intending to leverage it to improve operational efficiency. Gen AI (Gen AI) enables the industry to dig deeper into its data and extract valuable insights in a faster, easier, more accessible way. So, to learn more about harnessing Gen AI for workflow and maintenance optimization, we sat down with Partha Chatterjee, Director - Energy, Data and AI at MRE Consulting.
Read as he reveals practical strategies and lessons learned for operators looking to leverage Gen AI for real-time decision-making, with a vision for using Gen AI tools to streamline complex workflows.
Maryam Irfan, Oil & Gas IQ: Before we dive in, can you give us a little bit of background about yourself and your role as Principal, Data Analysis at Shell?
Partha Chatterjee: I have been in the technology field within the energy sector, covering upstream, midstream, and now downstream operations, for over 30 years. I started my career with Schlumberger, driving their first drilling expert system called Advisor.
My experience includes roles in nominations, scheduling, and pipeline management at Tenneco Gas, and subsequently Kinder Morgan. In the last seven years, I’ve started leading data analytics initiatives at Shell Energy Americas where I work on the trading and supply of natural gas, power, and LNG, with extensive involvement in renewables.
My passion lies in building a strong data culture and advancing data analytics, including AI and Gen AI.
Maryam Irfan, Oil & Gas IQ: What do you consider when determining which use cases to prioritize for operational optimization?
Partha Chatterjee: The first step is to identify use cases that are manually intensive. Gen AI is especially useful for scenarios requiring a deep understanding and explanation of text and images, where it can provide information back to users in a clear, actionable format. This applies to tasks like researching and understanding documents, images, operations manuals, regulations, market research, and other similar areas. Gen AI then translates this information into a comprehensible format so users can make informed decisions—whether in trading, logistics, equipment operations, or regulatory compliance.
These are the more straightforward use cases and from there, it can evolve into more sophisticated applications like sentiment analysis and predictive analytics. For example, it can combine subjective sentiments found online with quantitative data to aid in decision-making, optimizing trading logistics, managing supply chains, or forecasting demand and supply.
READ: Driving Innovation: Covestro’s Journey with Digital Twin Technology
Maryam Irfan, Oil & Gas IQ: How can operators effectively use Gen AI tools to help solve operational complexity challenges?
Partha Chatterjee: One area where Gen AI can be particularly useful is in understanding manuals and operating guidelines to aid in the actual operation of equipment. For instance, with IoT devices, Gen AI can interpret different signals to not only diagnose issues but also recommend solutions based on operating manuals. This provides operators with actionable guidance to effectively manage various types of equipment.
This capability is extremely helpful for interpreting signals and proactively identifying and addressing issues, preventing them from escalating into major problems.
More importantly, it is now able to work with both text and visual data, including videos and images. So, for example, if an operator encounters an error, they can take a picture of the equipment, allowing Gen AI to identify specific issues, such as a loose bolt or an improperly attached pipe. Once the problem is identified, the operator can consult the manual or even access step-by-step video instructions provided by Gen AI on safely removing and reinstalling components.
Maryam Irfan, Oil & Gas IQ: What are the key considerations when training Gen AI in industrial settings?
Partha Chatterjee: Firstly, AI is dependent on high-quality, diverse datasets, and having a continuous, varied dataset—not just a small, handpicked sample—is crucial. This means training AI models across a wide range of scenarios and use cases to ensure robust performance.
Secondly, it’s important to run extensive testing and pilot programs, ideally across different conditions over several months. For example, if we’re working with operational AI in industrial settings, testing in both winter and summer is essential. Machines may behave differently in hot, humid environments compared to dry, freezing ones, so simulating these conditions can help understand AI’s performance across varying situations.
One example is using AI to diagnose equipment issues via images. A camera may capture high-quality photos during the day, but the image quality might degrade in low-light conditions at night. Testing across lighting variations can help handle challenging conditions better.
Finally, testing should cover ‘limit cases’—scenarios that push the boundaries of AI’s capabilities. For instance, understanding complex conditions where multiple factors interact (such as one valve malfunctioning while another meter shows abnormal readings) is essential. These combinations add complexity, highlighting again the importance of a diverse, comprehensive dataset for training.
Maryam Irfan, Oil & Gas IQ: Despite the diverse data sets, and the trialling and testing, how can one ensure Gen AI models are providing accurate, safe, and reliable insights?
Partha Chatterjee: When beginning to use Gen AI, I recommend using it as an assistant with human supervision. There should be a human reviewing the instructions generated by Gen AI before pulling the trigger. This level of oversight is essential, especially in critical applications, to ensure the accuracy and reliability of outcomes. As confidence in the AI’s performance grows, the level of supervision can be reduced, but in high-stakes areas, we are not yet at a point where complete automation without human intervention is advisable.
While Gen AI can drive efficiency and reduce the need for certain manual tasks, human supervision ensures quality and reliability. This allows the team to shift their focus to more productive work while maintaining an essential layer of oversight.
Recently, we encountered a situation where Gen AI referenced an action based on a regulation that was set to take effect in the future. Although the AI’s interpretation was technically correct, the operator was able to identify that the regulation had been delayed. This level of contextual understanding is something only an experienced operator can provide and highlights why human supervision remains essential.
Maryam Irfan, Oil & Gas IQ: For operators looking to incorporate AI or Gen AI within their operations, what ROI can they expect?
Partha Chatterjee: I think, with Gen AI, the entire digital space can squeeze tremendous value. Take an operator’s work, as an example, even something as straightforward as understanding a manual. My estimate is that with Gen AI, we could see time savings of about 15–20% in the first year alone. And if implemented correctly, those savings could increase over time.
These gains come from Gen AI automating manual tasks, which currently require time-consuming interpretation and summarization of information.
Another area where we are seeing value in the AI and operational space is in predictive analytics and maintenance. Take, for example, equipment that traditionally requires maintenance every six months. This routine creates downtime and incurs labor costs. However, with predictive analytics, we can adapt that schedule based on actual usage conditions. In hot, humid environments, maintenance might be needed every six months, but in cooler, less humid environments, it could be extended to 18 months. This adjustment translates to significant cost savings by delaying unnecessary maintenance.
READ: Gen AI in Focus: How to Strategize in the Era of Technological Evolution
Maryam Irfan, Oil & Gas IQ: There is obviously a learning curve associated with a tool like Gen AI… What lessons have you learned from implementing Gen AI in operational settings and how has it shaped your current digital strategy?
Partha Chatterjee: One surprising insight we have uncovered is how even seasoned experts benefit from Gen AI. Initially, we thought Gen AI would primarily help new employees or those less familiar with certain operational or regulatory details. However, we discovered that even experts with 30 years of experience tend to use only 30–40% of their accumulated knowledge in practice.
For example, a piece of equipment might have three ways it can be repaired. An experienced technician may only use one method because it is familiar, though it may take more time and effort than the alternatives. Gen AI, however, does not have memory bias. It can provide every single option based on the tool or equipment’s sophistication, refreshing knowledge that might otherwise be lost or forgotten over time.
Another lesson is the importance of refining AI’s language to ensure accurate interpretation across different users and regions. We have observed challenges when language or terminology in manuals varies culturally or linguistically, so, it is crucial to optimize the language and tailor it to specific audiences.
Lastly, thorough testing across diverse scenarios is essential. Gen AI is often integrated with other systems, such as IoT devices, which might trigger alerts based on specific conditions. Running tests under different scenarios, covering all boundary and limit cases can help verify that the AI performs accurately across a range of conditions.
Maryam Irfan, Oil & Gas IQ: Lastly, I understand you are joining us at our upcoming AI in Energy Summit! What are you most looking forward to?
Partha Chatterjee: My top priority is to engage with experts, not only those specializing in Gen AI but also individuals on the operational and business side. I want to hear about their various use cases and then stimulate my thinking on how we can best address their various challenges.
I am also excited to learn about new tools and technologies that are emerging and understand the challenges these tools can address. Digital transformation is not merely a technology change; it is a business-driven initiative where technology serves as an enabler. It is crucial to choose the right technology for the specific business problem we are trying to solve. So, once I have insights into the use cases and available tools, I want to focus on how to select the best solutions.
We find ourselves in a time of technology abundance, so it is crucial for technologists like us—who also possess domain knowledge in the energy sector—to select the right AI and Gen AI solutions for the specific problems at hand.
Learn more about leveraging AI and data-driven technologies to enhance production, optimize asset management, improve sustainability, and reduce operating costs at our upcoming events:
AI in Energy Summit
February 24-25, 2025 | Houston, TX
The Connected Worker: Energy Summit
March 18-20, 2025 | Houston, TX
Operational Excellence in Oil & Gas
November 4-6, 2025 | Houston, TX