5 Things We Learned About the Connected Worker Last Week
Add bookmark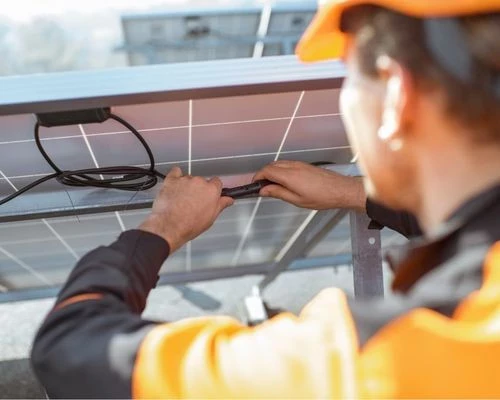
Leaders from across the industrial sector, including Delek US, Eastmann Chemicals, BASF, and many more, gathered at Oil and Gas IQ’s Connected Worker Summit recently to share case studies and best practices on what it takes to deploy connected worker platforms for measurable business benefits.
Here are 5 things we learned:
#1: User adoption is everything
You can deliver project that is on time and on budget, but, at the end of the day, the only metric that truly matters is whether your people adopt new tools and new ways of working. The end user should be engaged early and brought along on the journey.
#2: Resistance isn’t futile, it’s to be expected
Workers get used to operating within certain parameters and processes that have served them well in the past. The introduction of connected worker technology threatens the status quo. Resistance is to be expected; don’t be surprised by it. Instead, expect it and plan for it.
“You really have to anticipate that this is a perfectly natural human reaction that you're going to get from a subset of your population who don't want things to change,” observed Al Lindseth, Principal of C150 Advisory Services. “You have to manage them through that. You have to give them the reason for change. You have to identify those risks ahead of time and have mitigation plans in place.”
#3: Connected Worker is not just an IT project
It can be easy to get distracted by cool new technology. However, the non-technology elements – process, culture, organizational readiness – often matter more to a Connected Worker implementation. All elements must be considered as part of a Connected Worker rollout. How will you improve the underlying processes? How will your workers be brought along on the journey? How will you make sure the business is ready for the change?
#4: Foundational infrastructure is critical
It sounds basic, but too many organizations forget that they need to ensure connected worker apps will connect workers where they actually work. In industrial environments, that often means ensuring internet access in areas and locations where connectivity has traditionally been poor or non-existent. Make sure you’ve got connectivity and adequate bandwidth everywhere you expect workers to access digital connected worker platforms.
#5: It’s all about agility
The pace of change and volatility in the business environment today mean that organizations must be ready to adapt to changing circumstance. Digital solutions must follow suit. Introduce apps quickly, test out new ideas, fail fast if you’re going to fail, and move on.
Interested in learning more about this topic?
Join us at The Connected Worker Summit on March 28-30, 2023 and network with over 150 of your industry peers at the Norris Conference Center in Houston, TX., and learn how to evaluate the existing gaps in your connected worker capability and identify the data-driven solutions that will drive continuous improvement across your operations. Download the agenda here.