The Human Centered Connected Worker Framework
Add bookmark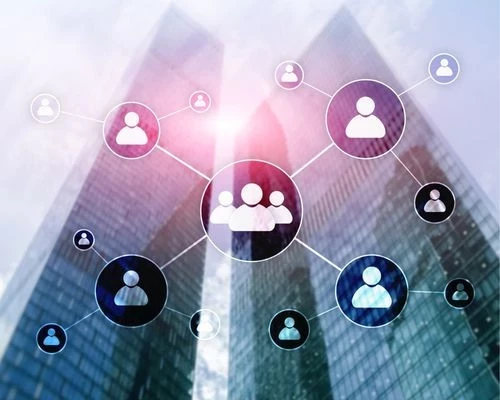
In part 1 of this series, I wrote about the need to shift from a technology focus to a human focus to address worker engagement, burnout, and labor scarcity. In this article, I will look at how you can achieve this by creating a human centered connected worker framework.
READ: Part 1: Can the Connected Worker Concept Solve the Great Workplace Disconnect?
Industry 4.0 Started as a Plant-Centered Revolution
Industry 4.0, also known as the fourth industrial revolution, started as a way to modernize manufacturing plants by increasing efficiency through cyber-physical connectivity. This movement is built on nine pillars of connected technology that aim to connect systems, provide information transparency, and automate decision-making and job tasks.
Revolutionizing the plant meant that organizations and vendors started by embracing the rise of digital industrial technologies to address the most pressing plant level opportunities. The plant and connected technologies were used as the “first principles” in design thinking.
However, as the smoke settles many are seeing that this scenario resulted in a top-down solution approach that has delivered some unintended consequences.
The Early Pains of Isolated products vs Integrated solutions
The connected plant - connected technology approach too often results in vendors promoting and selling isolated, available products rather than delivering complimentary and well-integrated solutions. Vendors advocate how broad software products will support safety, quality, efficiency, and productivity in terms of projects and plant operations. Simply put, since no single vendor or IOT platform has captured the market on end-to-end solutions, industry is often left with a “not so” connected mishmash. Since the plant is the big fish, individual workers typically experience the trickle-down impact of broad digital transformation investments.
This is especially worrisome given research shows that 80% of work environment issues impacting humans are embedded in the higher-level plant and process design phases.
To address the focus issue, it’s important for designers of connected worker solutions to move away from the assumption that the plant is the “first principle.” In connected worker solutions - the worker experience must be used as the “first principle” of design.
Measurement Systems Are Evolving
The trickle-down effect has been reinforced by the various maturity models aimed at measuring Industry 4.0 progress. Many solution providers and industry entities have created maturity models using high-level headings such as Industry 4.0, Connected Enterprise/Plant, Digital Plant, Smart Factory, Augmented Workforce, and Digital Transformation.
Many have also adapted the Capability Maturity Model (CMM), which is an IT-centric methodology that software developers use for process optimization. Other models measure progress in terms of plant or operational criteria such as an organization's ability to capture and assess production or how an organization handles predictive and preventative maintenance events.
The very few connected worker maturity models that exist today fail to measure the relevant factors that drive and enable more sophisticated human performance experiences. Instead, they frame connected worker systems in terms of levels of augmentation or technical capabilities.
The good news is that industry is recognizing the need for greater sophistication in measuring the subcomponents and enablers of the connected ecosystem. This can be seen in emerging maturity models for areas such as digital content metadata management and learning in the flow of work that are needed to deliver more refined and integrated end-to-end success.
Creating the Human Centered Connected Worker Framework
Given the number of pressing worker issues and low engagement levels, industry must recalibrate the connected worker concept. More focus is needed to reinvigorate the worker experience, address current pain points, and improve the overall nature of work in ways that make employees eager to come to work every day.
Addressing today’s issues requires the Industry 4.0 movement to mature and embrace the adoption of Human Centered Connected Worker Frameworks. For decades industrial organizational engineers and behavioral scientists have done the research to prove that human performance rises, and falls based on core dimensions related to the work environment and the individual worker.
While there are several frameworks that can be adapted for connected worker solutions, one effective approach is to adopt the Behavior Engineering Model (BEM) proposed by Thomas F. Gilbert (see Figure 1, below).
The BEM is a well-established framework that has been used to design and improve work systems for over 40 years. It includes a set of analytical criteria that help identify the critical factors that influence worker behavior, performance, and well-being.
This model can be adapted as a framework to measure the various subcomponents and enablers of the connected worker ecosystem. Gilbert’s model suggests that human performance in complex systems is a function of the interaction between both environmental and individual factors.
Other practitioners may prefer more targeted models such as Cognitive Engineering models. These models have historically been leveraged in the design of human-computer interactions for operators of complex and dynamic systems.
Like the BEM, Cognitive Engineering models leverage interdisciplinary fields that draw on knowledge from cognitive psychology, human-computer interaction, and artificial intelligence to design systems and technologies that are well-suited to human cognition and behavior. The BEM’s intent is to engineer human performance within an overarching social-technical work system, that also leverages the components of cognitive engineering.
Figure 1. Gilbert’s Behavior Engineering Model (BEM)
In their classic 1995 book “Improving Performance” Rummler and Brache suggested that 80% to 90% of performance improvement opportunity resides in the work environment, while 15-20% of the opportunities are in the Skills and Knowledge domain. They also found that fewer than 1% of performance problems result from individual capacity deficiencies. These type statistics as well as more recent studies highlight the impact that each of these six variables can have on human performance and worker experience.
It’s important to note that whatever model or framework is adopted, the strategic intent is to leverage what we know about the human condition to create more engaging, productive, and enriching worker experiences.
Driving the Next Level of Connected Worker Maturity
In conclusion, Industry 4.0 began as a plant-centered revolution, but it is now important to expand the focus to attend to the connected worker experience. Most will agree that up to and including today, connected solutions focus on freeing humans from dull, dirty, and dangerous tasks. However, if organizations truly want a human-centric approach for the connected worker, they need to move from simply automating away tasks and start implementing change that workers feel is "done for them" rather than “done to them."
By adopting a human-centered approach and using specialized maturity models, industry can create solutions that not only increase operational efficiency but also improve the overall nature of work for employees.
Applied thoughtfully, human performance engineering models can:
- help organizations diagnose the individual and environmental factors that management can control, in supporting worker achievement and employee experience
- address the factors that are creating frustration for today’s workers who seem to be collectively impatient, distracted, overwhelmed, and burnt out.
My next article will present relevant examples for connected worker solutions that integrate to collectively enhance and frame how the six-part BEM model can be applied.
Interested in learning more about this topic?
Join us at The Connected Worker Summit on March 28-30, 2023 and network with over 150 of your industry peers at the Norris Conference Center in Houston, TX., and learn how to evaluate the existing gaps in your connected worker capability and identify the data-driven solutions that will drive continuous improvement across your operations. Download the event agenda now.