Four Ways that Oil and Gas Companies Get Digital Transformation Wrong
Interview with Al Lindseth at The Connected Worker Summit
Add bookmark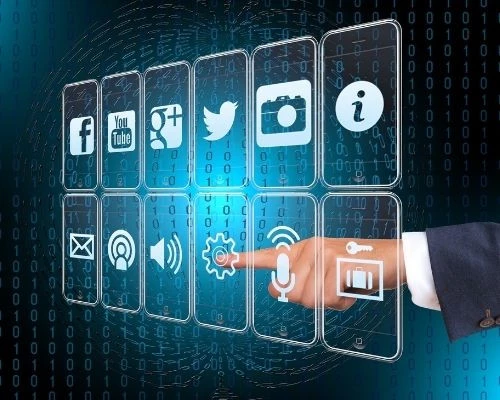
As technology provokes widespread changes in the oil and gas industry, how can you manage the risk of digital transformation failure?
Al Lindseth is a multiple award-winning CIO who knows a thing or two about risk management. For over 22 years he served in various functions at Plains All American Pipeline. In his most recent role he served as SVP of Technology, Process, and Risk Management.
Oil and Gas IQ’s Grant Schwer caught up with Lindseth, now principal of CI50 Advisory Services, at our recent Connected Worker conference to discuss where he sees companies going wrong with digital transformation, the role of people, process and culture, and how risk management can help.
Grant Schwer, Oil and Gas IQ: As we connect workers to operational processes with more digital devices we increase our cyber risks. How do you mitigate those?
Al Lindseth: The Colonial pipeline incident was probably the most transformative event that happened in midstream industry in the last couple of years. The incident, where hackers threatened the operational systems of the pipeline and led to a prolonged shutdown, was important in terms of the regulation that came out of it.
But cyber risk extends beyond cyber security. It’s also the risk inherent in transformative change efforts. You've really got to have recognize why they fail and then adapt your approach.
One reason that they fail is due to non-technological reason. You may have a great technology system and a great cybersecurity system, but there is a whole business ecosystem around it.
People, process and culture end up being a huge piece of your change effort. Something like 20% of the change relies on technology and the other is rooted in the people and process.
The challenge is that sometimes executives have their laundry list of technology projects and they leapfrog over the people and process side of things.
If you look at the numbers that we often throw around you hear that somewhere between 70-80% of digital transformation efforts fail.
Risk management can help. You need to identify our goals and what could keep you from achieving them. Those are your risks that you take steps to address.
To innovate, you must take risks. It’s difficult to create future value without taking risks.
Grant Schwer, Oil and Gas IQ: Here, at our Connected Worker conference, we’ve been talking a lot about the importance of culture. How do you see culture playing in?
Al Lindseth: We've seen a massive acceleration of technology over the last couple years. Even before COVID, cloud computing and big data were really starting to accelerate. During COVID you saw people trying to manage assets remotely and increase automation.
That has led to an increasing quality of apps. A lot of emerging technology solves many operator problems.
But you need to cut through the noise and find out what’s keeping the operators from actually being able to capture value in the technology. Digital transformation fails because companies don’t factor in the behavioral element. You have to make sure that you’re aligning the problems that people are having with the solutions.
Like what you're reading? Sign up to our bi-monthly newsletter for exclusive industry insight.
Grant Schwer, Oil and Gas IQ: Where do you find companies often go wrong in their approach to digital tools to transform operations?
Al Linsdeth: I think there are four basic reasons that companies go wrong.
The first reason is they don't deal with the non-technology pieces: people, process, and culture.
What tends to happen is that the CIO makes a list of all the technology deliverables. Then the business people make lists of all the business deliverables.
The one thing that neither team want to deal with are the behavioral challenges. You must tackle behavior because otherwise, it’s going to keep you from achieving your goals. If your people don’t use the technology or follow the process, you won’t have succeeded.
The second reason is not having an attack plan that deals with the most critical things first. I mentioned that risk management helps because it forces you to look at your objectives and the potential barriers to achieving them.
You have to work from top to bottom through your list. The earlier you identify issues, the lower the risks and the cheaper it is to fix them.
Another way that companies go wrong is that they tend to approach innovative experimental efforts with an overly structured approach.
For instance, one of the worst things you can do when different groups feel threatened by a change is to put them all together in a room. What happens is that they focus on their differences and achieve nothing of value. Projects, however, often start like this because project managers in a PMO organization have been taught to bring all the stakeholders together at the start of a transformation project.
In this case, you need a different approach. Who’s going to lead the change? Don’t just throw your PMO groups at it. When people are threatened by changes it doesn't work that way. You have to be more experimental; there's a difference between innovation and optimization of standards.
Once you get through a lot of those challenges – aligning people, process, and culture - you can start to apply the right techniques to the right situation.
Another reason is friction and resistance between different groups. When companies are trying to improve end to end processes, there can be challenges in the hand offs between groups. One group, which handles one part of the process, may not want to move forward with a project while another does.
You won’t get the full value of end-to-end process improvement if you don’t have all the relevant groups on board.
For instance, if you’re the head of engineering and you want to improve project management, you need to get the business development team on board. If they’re out there promising constant changes to requirements, you’re going to have challenges achieving your goals.
You have to look across all those key dependencies. If one group doesn’t want to be part of it, you might have to say that the project won’t move forward at all because we’re not going to see the value out of it.
WATCH: Future-Proof Plant Strategies – A How To Guide
Grant: What do you do when there are groups that are resistant to change?
Al Lindseth: Early on, you have to you have to test the organizational readiness for change. It actually isn’t very difficult to determine if a group is really open to change.
If you go through the right steps and they're not ready, then I don't think you move forward unless they get on board.
It can be a challenge when there are some groups that want to move forward and others that don’t. Some leaders may feel that they’re happy with the status quo and the project is threatening their kingdom. They’re not thinking about the big picture and how the organization as a whole will benefit by improving the process end-to-end.
This is particularly relevant when you’re looking at the connected worker. From a corporate perspective, you need to get different data to present to workers so they can do their job more effectively and efficiently.
But if you can only get data from some of your groups, it can cause the whole project to fail. The guys at the plant look at the data and it doesn’t have the most important information that they need because as your different groups didn’t sit down together to figure out what was of most value to provide to the workers.
You need to expect that there will be resistance to change in your projects and you need to manage for that. It's a natural human reaction for people to want to preserve what they have.
On the business side we manage risk by hedging and trading and we need to take a similarly thorough approach to changing people.
Interested in Learning More?
The global pandemic and economic crisis has put an even stronger emphasis on the importance of operational excellence. Yet as oil and gas companies respond and adapt to the new normal, many are redefining what operational excellence means to them.
Now in its 13th year, the Operational Excellence in Oil & Gas Executive Summit brings together over 100 senior level executives to the Norris Conference Center November 1-3, 2022. Innovators like Shell, Equinor, Chevron, Plains All American, Delek and more will each share their own transformation journey. Find out more here.